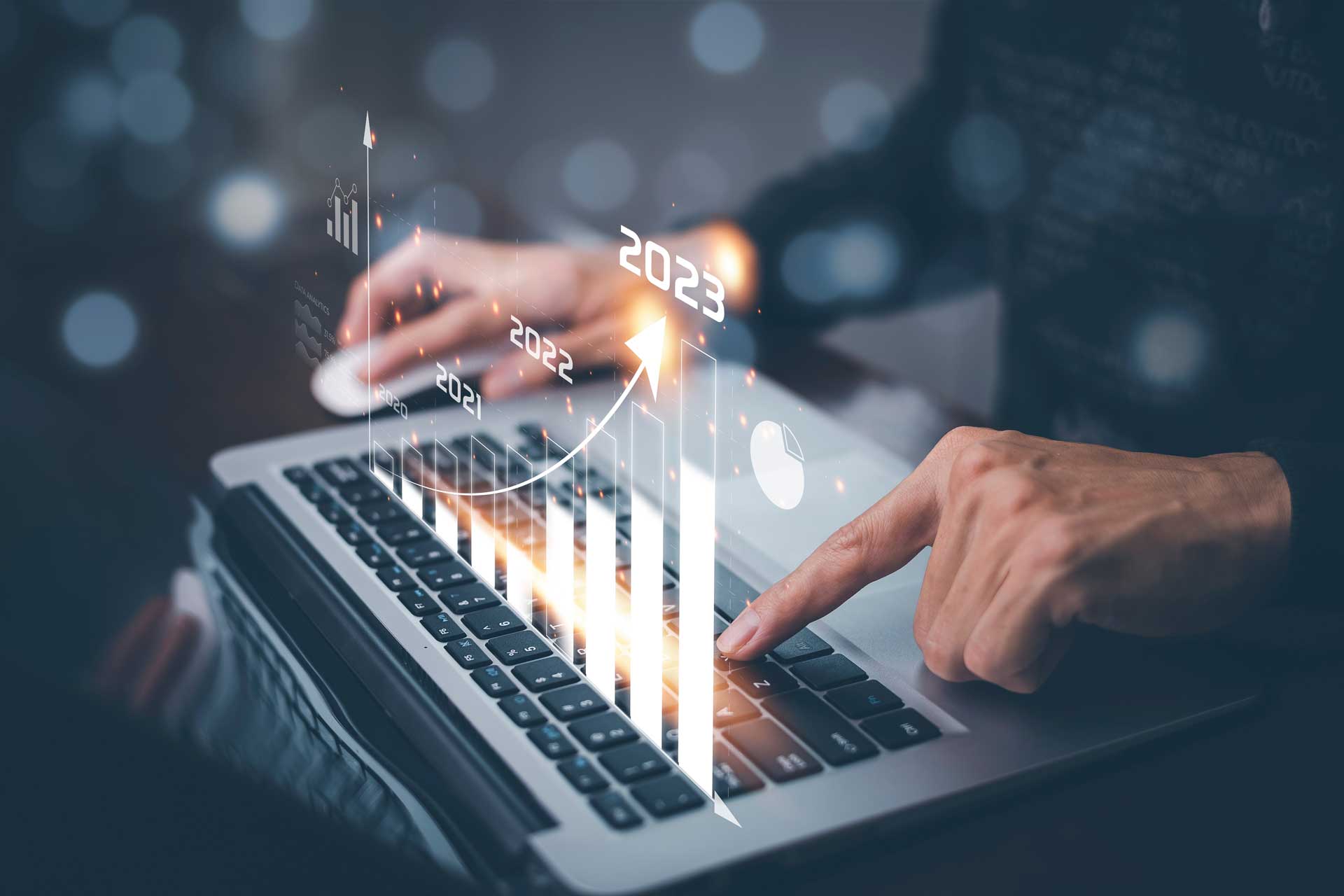
As you work on your strategic plans for 2023, is predictive maintenance on your radar? If not, perhaps it should be.
Entering another year of economic uncertainty, business leaders are coming together to define their overall strategy and goals to maximize potential and results in the next year, the next five years, and over the long-haul. At the same time, they have a keen eye on spending and investments – what’s worth it and what can wait.
While equipment and machine maintenance may seem too tactical for an overall business plan, it does fall under a few key strategies that are shaping the future of manufacturing and setting the stage to distinguish between those operations that will survive versus thrive – namely, digitalization and operational excellence – both of which are at the heart of predictive maintenance.
According to BusinessNewsDaily, “Predictive maintenance is the practice of monitoring equipment via sensors, software and data feedback to prioritize equipment for proactive maintenance. It takes preventive maintenance one step further by streamlining the process of identifying which equipment (or even which components) is showing signs of needing attention.”
To put it another way, you use technology and data to more accurately learn when equipment or machinery isn’t performing up to par and needs to be fixed or replaced – before it causes issues or, even worse, a shutdown. It sounds like current preventive maintenance strategies. The difference? With predictive maintenance, you know something is not performing on par and needs to be addressed. With preventive maintenance, you’re investing time, resources, and money in something that may or may not be needed.
Predictive maintenance uses Internet of Things (IoT) devices and sensors to collect data – like vibrations, temperature, and lubrication — from equipment.
The data is fed to a central place where algorithms are used to help machines learn to identify if maintenance is needed or a breakdown is coming. That way, maintenance work can be prioritized and resources dispatched where and when they can make the biggest impact.
According to Due.com, “Research shows that the average manufacturer deals with 800 hours of downtime per year – or more than 15 hours per week – and the costs can be outrageous. Just for perspective, consider that the average automotive manufacturer loses $22,000 per minute of downtime. While your costs likely don’t come anywhere close to this, even losing a few hundred dollars per hour can have a significant impact on your bottom line.”
There’s a lot of potential to use maintenance for a strategic and competitive advantage.
ChiefExecutive.net notes, “81 percent of manufacturers are aware of the potential for machine learning to enhance maintenance, but only 17 percent have implemented programs to put those principles into action.”
The impact is far-reaching. It can help increase productivity, increase the longevity of machines and equipment, and decrease shutdowns and resulting impacts on customer relations. Still, it’s hard to justify investing in a new approach to maintenance given current economic uncertainties; on the other hand, can you afford not to?
Look at your current maintenance, supply chain (for equipment and parts), and talent challenges and costs.
Are they increasing? Will designating more money solve the issues at hand or is there a more balanced way to manage these issues in the short-term while setting the stage for a more successful long term?
For example, we know the global talent shortage is not going away. In fact, it’s only going to get worse. As reported in CFO.com, “Korn Ferry estimates the global human talent shortage will reach 85 million people by 2030. Private organizations and governments will be challenged like never before to help find ways to accelerate their development processes and build expanded talent acquisition capabilities.”
While increasing pay rates, enhancing benefits packages, and investing in retention can help, they still don’t address the long-term issue.
There are not going to be enough people to do all the work required. The solution? Change how work gets done through digital solutions, like predictive maintenance.
Although we can’t tell you which predictive maintenance solutions to use – we’re accountants, tax experts, and auditors, we can help you understand the financial benefits, opportunities, and impact of investing in predictive maintenance as part of your organization’s digitalization strategy in 2023 and beyond. Interested? Contact RBT CPAs today.