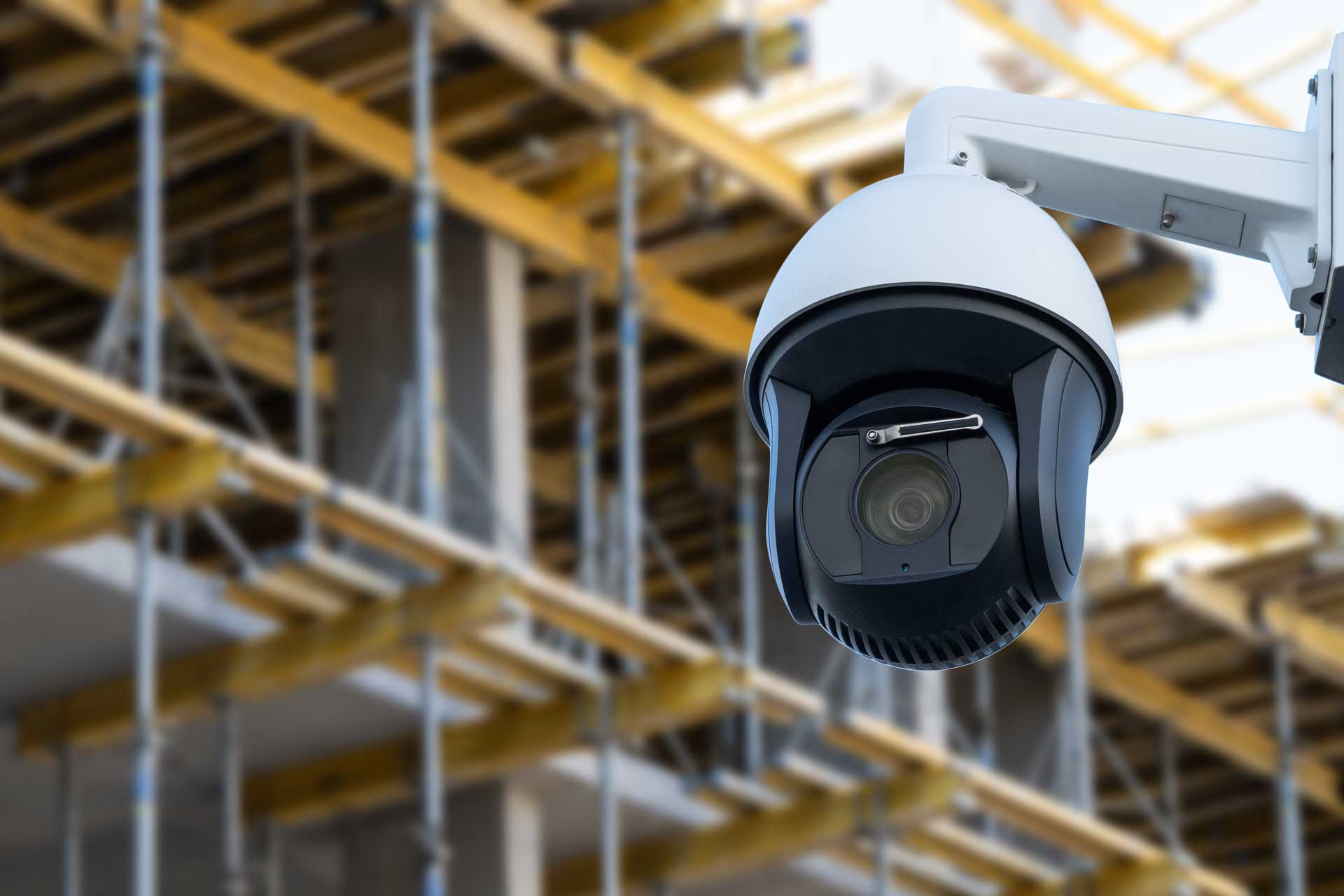
The National Equipment Register (NER) places the annual cost of losses due to equipment theft at up to $300 million for residential construction sites and $1 billion for commercial sites, with a $30,000 average price tag per theft. Beyond the actual cost, equipment theft can significantly add to the challenge of completing a project on time and in budget; hurt your reputation; drive up insurance; tie up cash and credit renting or buying replacements; and cause you to miss out on future business opportunities. While there are no guarantees, having a comprehensive anti-theft plan can turn the odds in your favor.
According to TheRepublic.com, “The people who do the stealing range from individuals committing small-time, spur-of-the-moment thefts to organized crews who go from state to state, hitting construction sites and then blowing town.” Top heavy equipment thefts according to Tenna.com include skid steers; wheeled and tracked loaders; towables; backhoes; tractors; wheel loaders; utility vehicles; UTVs; excavators; forklifts; bulldozers; rollers; generators; welders; and compressors.
Especially if the work site is in a remote location or the job timeframe includes extended periods of inactivity (i.e., a long holiday weekend), a comprehensive strategy can help reduce the chance of equipment theft. Here are some tips to consider:
- Create a job site security plan and assign security-related responsibilities. Have your team spend time at the start of a project identifying and addressing potential security weaknesses.
- Prequalify contractors before hiring them. According to LevelSet, most theft happens internally and subcontractors can easily identify your weak spots.
- Have a system to ensure only approved personnel enter the work site (i.e., photo ID badges).
- “Mark your equipment with an identification system, such as a driver’s license number (state initials, number, followed by DL). This is the only traceable number in all 50 states. Put numbers in two spots: one that’s obvious and one that’s hidden.” (Source: Great American Insurance Group.)
- Take inventory. For all equipment and tools that will be used at a site, create an inventory including a photo, name, description, serial number/VIN, date of purchase, worksite, and who is approved to use it.
- Invest in equipment-related technology. GPS asset tracking hardware, operating systems, video telematics (with forward and rear-looking dash cams), and geolocation technology as a standard feature on new equipment (OEMs are increasingly offering it) can help you see where equipment is, get alerts when it turns on or moves, and more.
- Register heavy equipment with the National Equipment Register (NER), an organization that manages a database with detailed information about equipment ownership and potential matches with theft reports to help facilitate information sharing with insurers, equipment owners, and law enforcement.
- For smaller equipment, create a storage area. Assign and label a space for each piece so you can quickly and easily see when something is missing.
- Disable or make large equipment difficult to remove from a site. ConExpoConAgg suggests removing fuses and circuit breakers; and installing fuel shut-off equipment, wheel locks, battery switches, ignition locks and other deactivation devices. Also park equipment in a wagon-train circle and place easier to move pieces like generators in the middle.
- Create a check-in/check-out procedure. Have workers sign out equipment as they use it and sign it back in when finished.
- Set a policy to report any theft or vandalism to management immediately, so there’s a greater chance of recovery (which is said to happen only 25% of the time).
- Adopt additional security measures. Security cameras, fencing and access control systems, lighting and security guards help deter theft and can provide proof should a theft occur. Engaging local law enforcement and crime stopper groups to report anything suspicious outside of normal hours of operation can also help.
- Create an end of day security checklist. Is all equipment properly locked away/secured? Are lights, motion sensors, and security equipment turned on and working? Is the perimeter fence solid and secured? Have all entryway locks been closed and double-checked?
- Train employees and contractors on your equipment management plan and security protocols.
While developing a plan to keep an eye on your worksite equipment and machinery, you can count on RBT CPAs to keep an eye on your accounting, tax, audit, and business advisory needs. Interested in learning more? Give us a call.
RBT CPAs is proud to say all of our work is prepared in the U.S.A. – we never offshore. As a result, you get peace of mind that your operation’s financial and confidential information is handled by full-time, local staff who have met our high standards for quality, ethics, and professionalism.