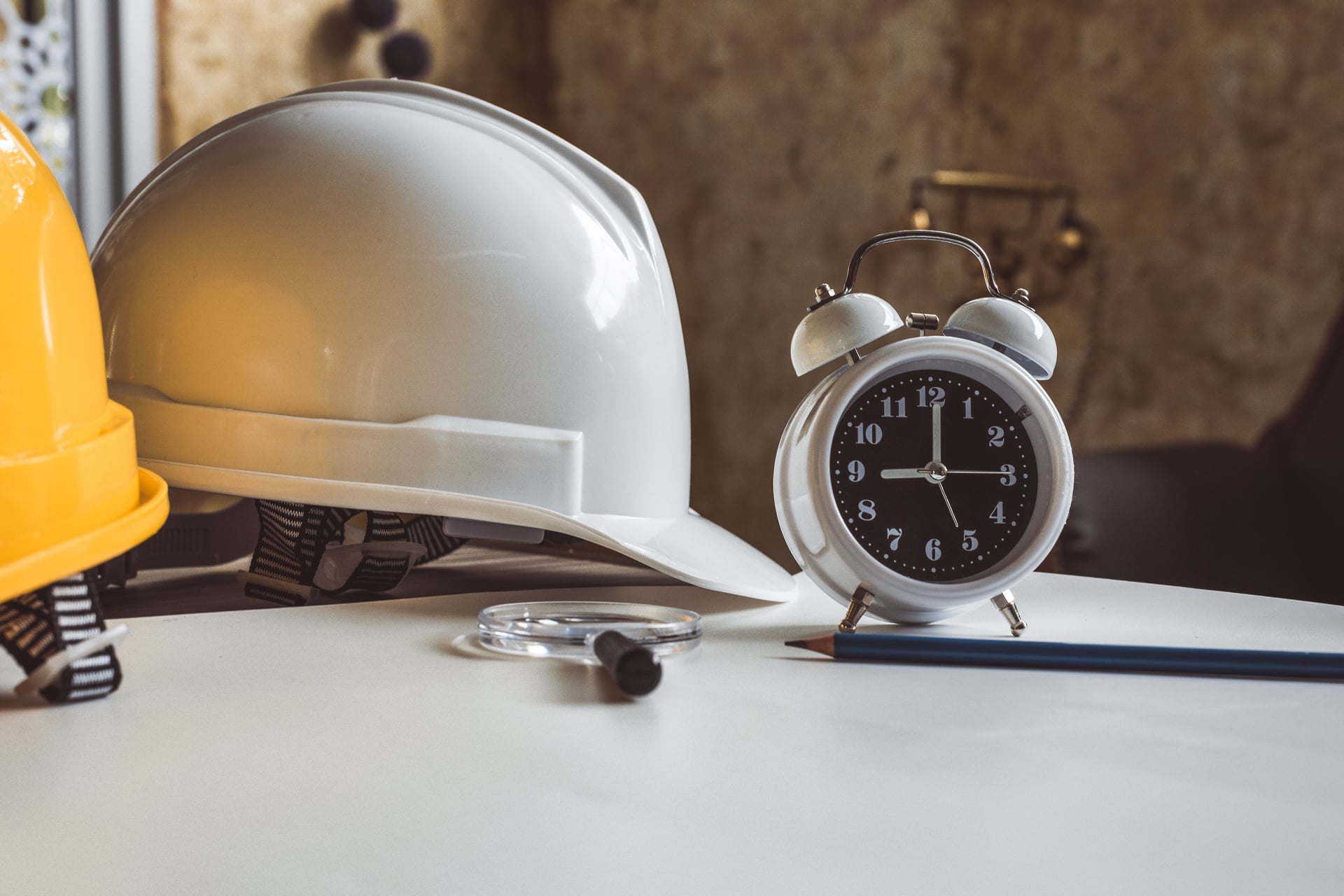
From inclement weather, to strict building code regulations, a shortage of skilled workers, material cost increases, and supply chain disruption – a lot of variables threaten to slow down the completion of construction jobs in the Northeast.
Not to mention, these roadblocks exist before factoring in the COVID-19 pandemic that has rocked the world economy. So, what happens to construction job completion timelines in New York when the global supply chain experiences shortages, delays and total operational shutdowns? Let’s dive into the lasting effects the construction industry is dealing with, and contemplate what lies ahead.
Many have drawn parallels between The Great Recession of 2007 and the pandemic we are currently experiencing.
The main difference: COVID-19 didn’t just disrupt the U.S. economy, it threw a wrench into the global supply chain process. There is also an acute uncertainty surrounding the possibility or inevitability of a second wave of COVID-19 later this year and into 2021. Contractors are left to navigate constantly changing safety protocols mandated by local and state government. In some instances, this means contractors must prepare for automatic project delays caused by social distancing measures and decreased worker capacity on job sites.
Contractor expectations of recovery vary by region.
The most recent survey conducted by The Associated General Contractors of America found because of the pandemic, 60% of responding firms have at least one future project postponed or canceled, while 33% reportedly have projects halted altogether. The share of firms reporting canceled projects has nearly doubled since the survey AGC conducted in June. Specifically in the Northeast, 45% of AGC survey respondents expect it will take more than six months for their firm’s volume of business to return to normal, while those in the West, South and Midwest expect they will bounce back faster.
Work is resuming.
New York updated its “essential businesses” considerations back in April to include not just healthcare facilities and emergency repairs but roads, bridges, some public school projects, municipal facilities, and energy projects as well. As of June, 33,556 previously closed non-essential sites were allowed to resume construction activity as part of the Phase 1 reopening, according to the New York City Department of Buildings. But global manufacturing plant shut downs meant tacking on additional weeks or months long delays on the local level. In the roofing industry for example, production in mainland China – where nearly 70% of the world’s solar roofing panels are manufactured – was completely shut down in the spring. Production of aluminum, plastic, slate, timber and rubber all declined worldwide since the early weeks of the outbreak.
So is there light at the end of the tunnel? The problem is that we are currently in the middle of the tunnel.
As the world waits on a reliable, widely available COVID-19 vaccine, only time will tell. But according to the most recent JP Morgan survey released this September, August saw manufacturing output increase for the second month running, following a five-month sequence of decline. Production rose and growth accelerated to a 16-month high at consumer goods producers and to 30- and 23-month peaks in the intermediate and investment goods categories respectively. China, the US, Germany, the UK, India and Brazil were some of the larger industrial nations to register expansions of output during August.
The long-term effects of the current crisis have yet to play out.
Contractors that double down on innovation efforts like a heightened focus on lean construction, workforce training or remote collaboration technology, will emerge more resilient. The best defense for contractors of any size operation is to actively evaluate their own supply chains to pinpoint vulnerabilities, identify potential alternative supply sources, prepare for steady cost bumps, and make sure they have adequate provisions in their contracts to protect themselves from the interruptions the ongoing coronavirus crisis creates.