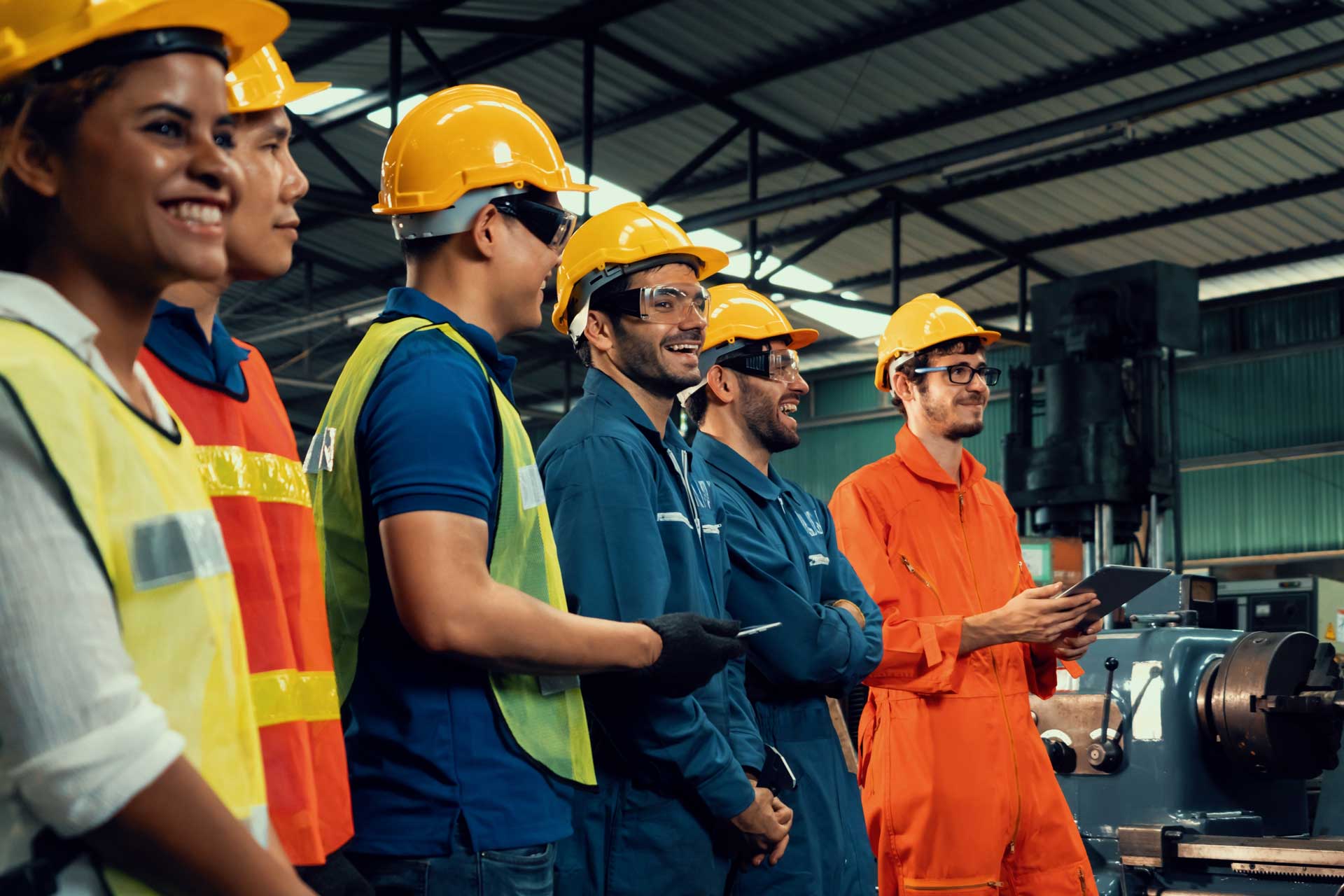
Manufacturing’s fourth industrial revolution, driven by artificial intelligence, cognitive automation, advanced robotics and analytics, and the Internet of Things (IOT) changing how work gets done and driving the need for more technology-savvy workers and skillsets. While employers have been preparing for changing workforce demographics for decades, none could have predicted the pandemic and its impacts on the workplace, including the great resignation, where employees are leaving the workforce in droves and holding employers to higher standards.
The pandemic combined with a generational shift in values has turned the labor market into an employees’ market, leaving employers to figure out what they need to do to compete for and win valued talent. As Baby Boomers retire, Millennials and Gen Zers are rising through the ranks with different values, redefining the workplace to account for things like work life balance, health, and job satisfaction. Every industry – including manufacturing – is being challenged to not only successfully create the future of work, but also to do it in a manner that considers very different generational mores than in the past.
As highlighted in a joint study conducted by global consulting firm Deloitte and The Manufacturing Institute, the industry is facing the largest talent shortfall ever, with an estimated 2 million jobs unfilled between 2015 and 2025, leaving employers to answer:
- How are manufacturing jobs and careers evolving?
- What skills are necessary for the future of work?
- What should manufacturers be doing to develop a talent pipeline where employees have the skills to work alongside advanced technologies?
These questions and the challenges prompting them have even made it to the White House, with a push for immigration reform that will help manufacturers attract and retain STEM talent for the future.
They also prompted The National Association of Manufacturers and the Manufacturing Institute to launch Creators Wanted in 2021 [LINK TO www.creatorswanted.org] – a campaign to change perceptions about manufacturing jobs and build a talent pipeline. Focusing on workforce development among students, women, veterans, underrepresented communities and more, the campaign includes online events and content, as well as a nationwide tour to educate students, parents, workers, and community leaders about modern manufacturing.
In the Hudson Valley, the Council of Industry manufacturing association has multi-faceted, collaborative strategies addressing these issues in our region. From training programs and workforce development to networking, advocacy and more, the council offers comprehensive solutions for manufacturing organizations and members in our communities. Resources include:
- Training A certificate program to train supervisors to lead; Hudson Valley Consortium Training, where six community colleges offer subsidized manufacturing related classes and certificates; and regulatory refresher training.
- Workforce development A regional workforce development strategy; New York State Manufacturers Alliance Apprenticeship Program (NYMAAP) providing on-the-job training and additional instruction for those participating in three- to four-year apprenticeship programs (see more information below); the Recruiting Initiative campaign to market manufacturing jobs in the region and help local companies recruit talent; the Hudson Valley Pathways Academy, a program targeting grades 9 to 14, leading to an Associate Degree and building a talent pipeline; National Manufacturing Day events; connecting students with manufacturers and engineers; and org, a program to educate about modern manufacturing opportunities and career paths.
- Networking Events to help manufacturing companies connect about business, Human Resources or Environmental Health & Safety, as well as special events.
- Surveys & Data Participate in a regional survey to learn about pay and benefit practices, which come into play when creating rewards strategies to attract and retain talent.
- Advocacy From Albany to Washington.
Of particular note is the Manufacturers Intermediary Apprenticeship Program (MIAP), which was created by the New York State Manufacturers Alliance of which the Council of Industry is a founding member and program administrator in the Hudson Valley. The program connects future skilled workers with small, medium, and large employers to secure paid apprenticeships in high-demand, competitive wage occupations, while completing their education.
Johnnieanne Hanson, Vice President of the Council, says interest in MIAP has grown during the pandemic, which likely put a brighter spotlight on recruiting and retention challenges. “What makes our program unique is that we’ve already done the legwork to create it. Employers don’t have to do anything other than express interest and start with even just one apprentice. So, it’s really appealing and do-able for a small to medium sized business that may otherwise not have the resources to build an apprenticeship program from the ground up.”
There’s also an abundance of financial support and incentives to get the ball rolling. “There’s money towards community college, tax credits, online learning licenses and grants for trainees,” Johnnianne says. “It’s a great time in terms of employers and employees have resources and support.”
The program can be used to attract new employees, incentivize new hires, and engage longer-term employees. “By investing in an employee, an employer is showing that it values the person, what they can contribute and their potential for the future. We’ve seen people who go through the program come out so happy and with such a sense of pride about the company investing in them. It means more than most realize,” Johnnianne adds.
The certifications can be viewed as the equivalent of a earning a college degree, while learning on-the-job skills and making an impact – two big values of the Millennials and Zers. In turn, employers set themselves up to retain and develop high potential talent.
“As the saying goes, ‘The best time to plant a tree is 20 years ago; the next best time is today.’ So, while employers should have been preparing for the talent crunch decades ago, it’s not too late to become part of the apprenticeship program. It starts with just a phone call,” Johnnieanne concludes.
No doubt, there has never been a more exciting or challenging time in manufacturing. RBT CPAs are here to partner with you on everything accounting and tax-wise, so you’re freed up to focus on creating a strong talent pipeline and business for the future. Let us know what we can do for you.